Formowanie wtryskowe to popularna metoda kształtowania tworzyw sztucznych wykorzystywana w wielu obszarach przemysłu. Do jej realizacji niezbędne są formy wtryskowe dostosowane do danego procesu. Zależnie od projektu i wymagań mogą one różnić się budową, kosztem i zastosowaniem – co warto wiedzieć na ich temat?
Zapytaj o wycenę
Czym jest forma wtryskowa?
Forma wtryskowa to specjalistyczne narzędzie wykorzystywane w procesie wtryskiwania tworzyw sztucznych. Jej głównym zadaniem jest nadanie kształtu wypraskom poprzez precyzyjne odwzorowanie geometrii detalu. Konstrukcja formy obejmuje szereg skomplikowanych elementów, z których kluczowe znaczenie mają powierzchnie formujące:
- stempel (część ruchoma);
- matryca (część nieruchoma).
W zależności od konstrukcji forma może być jedno- lub wielogniazdowa, co oznacza możliwość produkcji jednej
bądź wielu wyprasek w pojedynczym cyklu. Proces wtryskiwania polega na wtryskiwaniu uplastycznionego tworzywa do gniazda formy, gdzie ulega ono schłodzeniu i przyjmuje docelowy kształt.
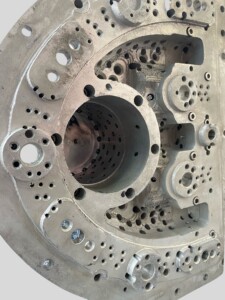
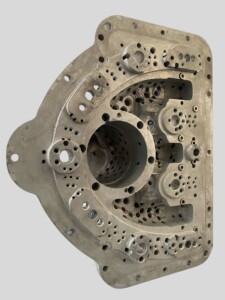
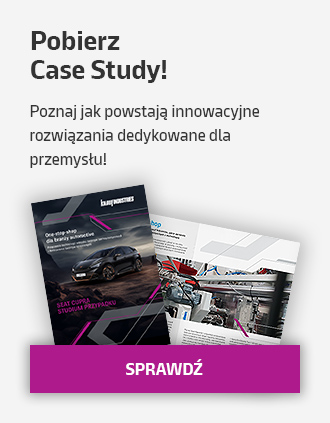
Budowa i kluczowe elementy formy wtryskowej
Nowoczesne formy wtryskowe składają się z wielu precyzyjnie wykonanych komponentów, których jakość wpływa bezpośrednio na efektywność procesu oraz parametry gotowego detalu. Do podstawowych elementów formy należą:
- Gniazda formujące – to zasadnicza część formy, która decyduje o geometrii wytwarzanej wypraski. Ich precyzyjne wykonanie i odpowiednia obróbka powierzchniowa zapewniają powtarzalność oraz wysoką jakość produktów.
- Układ wlewowy – Odpowiada za doprowadzenie uplastycznionego tworzywa do gniazda formującego. Jego optymalne zaprojektowanie ma kluczowe znaczenie dla równomiernego wypełnienia formy oraz eliminacji wad wyprasek, takich jak:
• Niedolewy,
• Pęcherze powietrza,
• Wypływki.
- Układ chłodzenia – temperatura wypraski po wtrysku może sięgać nawet kilkuset stopni Celsjusza, dlatego efektywne chłodzenie formy jest niezbędne do skrócenia cyklu produkcyjnego i poprawy jakości detalu. Układ chłodzenia składa się z kanałów przepływowych, którymi cyrkuluje medium chłodzące (np. woda lub olej).
- Układ wypychania – zawiera zespół elementów odpowiedzialnych za bezpieczne usunięcie gotowego detalu z formy. W jego skład wchodzą wypychacze, tuleje i inne mechanizmy wspomagające automatyczne oddzielenie wypraski, zapobiegając jej uszkodzeniu.
- Elementy prowadzące –obejmują tuleje, kołki oraz prowadnice, które zapewniają precyzyjne centrowanie i płynne działanie formy w cyklu produkcyjnym. Ich właściwe wykonanie minimalizuje ryzyko zużycia oraz utrzymuje wysoką powtarzalność procesu.
- Obudowa formy– stanowi ochronę dla wewnętrznych komponentów i odpowiada za prawidłowe mocowanie formy w wtryskarce. Wykonana jest z wysokogatunkowej stali narzędziowej, co zapewnia jej trwałość i odporność na ekstremalne warunki pracy.
Koszt wykonania formy wtryskowej – co wpływa na cenę?
Koszt produkcji formy wtryskowej zależy od wielu czynników, a jego oszacowanie wymaga analizy parametrów technicznych oraz skali produkcji. Typowe przedziały cenowe kształtują się następująco:
- proste formy jednogniazdowe: od kilku do kilkunastu tysięcy złotych;
- zaawansowane formy wielogniazdowe: od kilkudziesięciu do nawet kilkuset tysięcy złotych.
Najważniejsze czynniki wpływające na koszt formy wtryskowej to:
- Rozmiar i skomplikowanie konstrukcji – większe i bardziej złożone formy wymagają większej ilości materiału oraz dłuższego czasu obróbki.
- Rodzaj użytej stali – formy produkowane są zazwyczaj ze stali narzędziowej, jednak w niektórych przypadkach stosuje się stopy o podwyższonej odporności na ścieranie i korozję.
- Liczba gniazd formujących – formy wielogniazdowe pozwalają na produkcję większej liczby detali w jednym cyklu, co znacząco obniża jednostkowy koszt produkcji, ale podnosi początkowe nakłady inwestycyjne.
- Zastosowanie systemów gorącokanałowych – ograniczają ilość odpadów i skracają cykl produkcyjny, jednak ich wdrożenie zwiększa koszty początkowe.
- Koszty projektowe i symulacje przepływu materiału –szczególnie istotne w przypadku skomplikowanych form,
wymagających precyzyjnego zaprojektowania układu chłodzenia i wlewowego.
Masz pytania o wycenę? Napisz do nas korzystając z formularza kontaktowego.
Proces produkcji formy wtryskowej
Produkcja formy wtryskowej obejmuje kilka kluczowych etapów:
- Projektowanie CAD – opracowanie modelu 3D formy z uwzględnieniem wymagań technologicznych i parametrów procesu.
- Analiza przepływu tworzywa (MoldFlow) – symulacja wypełniania gniazda formy, pozwalająca zoptymalizować
układ wlewowy i parametry procesu.
- Obróbka CNC i EDM – precyzyjne frezowanie, toczenie oraz elektrodrążenie zapewniające dokładność odwzorowania
kształtu formy.
- Montaż i testy – finalne składanie komponentów oraz próby technologiczne na wtryskarce, mające na celu eliminację
potencjalnych błędów.
Rodzaje form wtryskowych
W zależności od specyfiki produkcji, wyróżnia się kilka podstawowych typów form wtryskowych:
- Formy zimnokanałowe – prostsze w budowie, generujące większe ilości odpadów produkcyjnych.
- Formy gorącokanałowe – wyposażone w systemy grzewcze, pozwalające na eliminację wlewków i redukcję strat
materiałowych.
- Formy jednogniazdowe – przeznaczone do produkcji pojedynczych detali w jednym cyklu.
- Formy wielogniazdowe – umożliwiają jednoczesne wytwarzanie kilku identycznych wyprasek.
- Formy piętrowe (stack mold) – składające się z kilku poziomów gniazd formujących, co zwiększa wydajność i pozwala na optymalne wykorzystanie przestrzeni roboczej maszyny.
Zastosowanie form wtryskowych w różnych branżach
Technologia wtrysku znajduje szerokie zastosowanie w wielu gałęziach przemysłu, m.in.:
- Automotive – elementy wnętrz pojazdów, panele, zderzaki.
- AGD/RTV – obudowy urządzeń, części mechaniczne.
- HVAC – komponenty systemów wentylacyjnych i klimatyzacyjnych.
- Przemysł meblarski – elementy konstrukcyjne i dekoracyjne.
Inne metody obróbki tworzyw sztucznych
Warto mieć na uwadze, że formowanie wtryskowe to tylko jedna z wielu metod obróbki tworzyw sztucznych stosowanych obecnie w przemyśle. Rozwiązania tego typu obejmują wiele procesów, które mogą być z łatwością przystosowane do konkretnych wymagań. W ramach oferty Knauf Industries można liczyć m.in. na wsparcie w procesach overmoldingu, wtrysku 2K (dwukomponentowego) czy też wtrysku sekwencyjnego. Przy każdym zadaniu zachowujemy maksymalną precyzję i przywiązujemy szczególną wagę do prawidłowego projektowania, co pozwala nam zaoferować najwyższe standardy jakości niezależnie od potrzeb klientów.
Knauf Industries – Twój partner w produkcji form wtryskowych
Knauf Industries oferuje kompleksowe wsparcie w zakresie projektowania i produkcji form wtryskowych. Dzięki
nowoczesnym technologiom oraz doświadczeniu w branży gwarantujemy najwyższą jakość i optymalizację procesów.
Skontaktuj się z nami, aby omówić szczegóły współpracy i zoptymalizować swoje procesy produkcyjne.
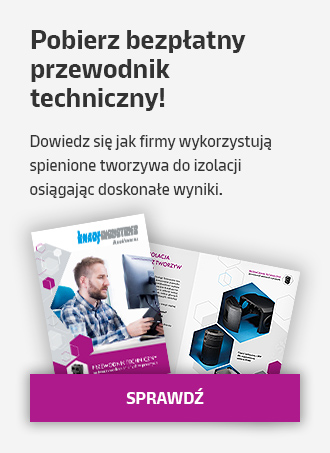
Chcesz zoptymalizować swoje procesy? Wypełnij formularz i sprawdź, jak możemy Ci pomóc.